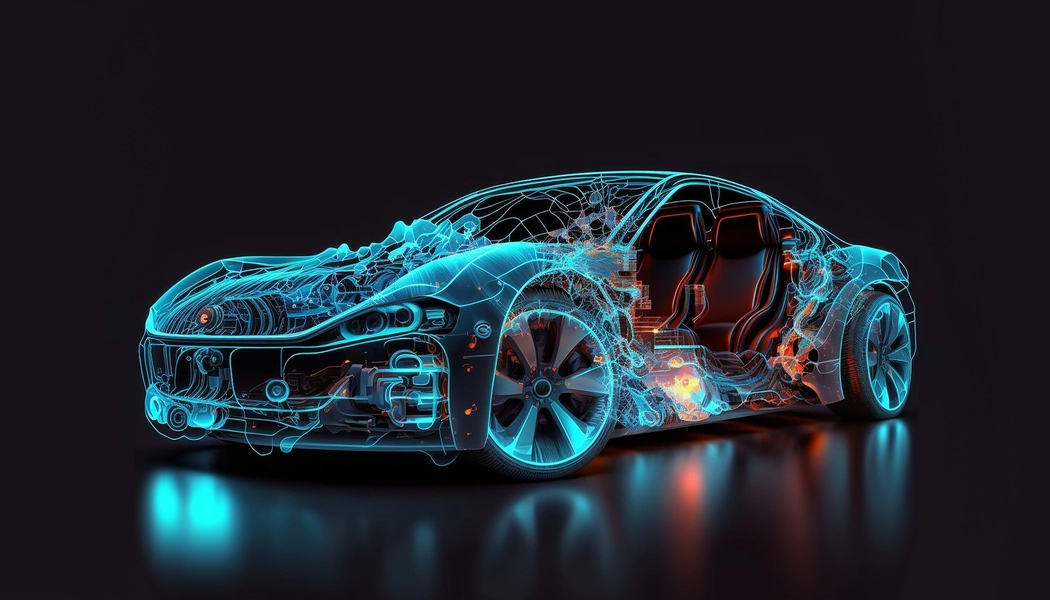
The Automotive Industry demands materials with high performance and durability standards. The reliability and longevity of vehicles are directly related to the quality of the materials used. Rubber materials are widely preferred in the automotive sector for their flexibility, durability, chemical resistance, and heat tolerance. These materials are used in various parts of vehicles, enhancing both driving safety and user comfort.
Key Rubber Materials Used in the Automotive Sector and Their Properties
EPDM (Ethylene Propylene Diene Monomer): EPDM rubber is known for its resistance to ozone, UV rays, and high temperatures. It is commonly used in automotive applications such as weather seals, window seals, and door gaskets that are exposed to external environments. Its water and chemical resistance also make it suitable for parts used in challenging conditions like engine compartments.
Nitrile Rubber (NBR): Nitrile rubber offers high resistance to petroleum-based oils and fuels. This property makes it ideal for components in contact with petroleum products, such as fuel hoses, engine seals, and various sealing elements in the automotive sector.
Silicone: Silicone stands out for its high-temperature resistance and flexibility. It is used in high-temperature areas of vehicles, such as engine compartments and cooling system hoses and gaskets. Silicone rubber retains flexibility even at low temperatures, making it particularly advantageous in cold climates.
Neoprene (Chloroprene Rubber, CR): Neoprene rubber is resistant to oil, heat, ozone, and weathering. It is commonly used in suspension systems, chassis components, and engine mounts, where vibration damping and high durability are required.
Fluoroelastomer (FKM): FKM rubber provides excellent resistance to high temperatures and chemicals. It is typically used in exhaust systems, turbo hoses, and other components in the engine area that require heat resistance. FKM maintains flexibility at high temperatures, ensuring consistent vehicle performance.
Applications of Rubber Materials in the Automotive Industry
Sealing Gaskets: Rubber materials are used to ensure sealing in vehicles. Components like window seals, door gaskets, and hood seals are made from materials such as EPDM and silicone rubber. These materials prevent water, dust, and air infiltration into the interior, enhancing comfort and safety.
Fuel and Cooling System Hoses: Hoses for transporting fuel, oil, and coolant in vehicles are made from materials such as NBR, FKM, and silicone rubber. These hoses resist chemicals and temperature variations, ensuring safe and reliable fluid transmission within the vehicle.
Engine Mounts and Suspension Systems: Rubber’s vibration-damping properties make it ideal for use in engine mounts and suspension systems. Materials such as neoprene and polyurethane absorb road shocks and vibrations, improving ride comfort.
Exhaust System Components: FKM and silicone rubber are used in exhaust systems due to their heat resistance. These materials ensure long-lasting and safe operation by withstanding hot gases and chemicals in the exhaust system.
Brake and Hydraulic System Components: Rubber components used in brake systems play a critical role in pressure resistance and flexibility. Nitrile rubber and polyurethane are used in hydraulic brake hoses and sealing elements, ensuring reliable performance even under high pressure.
Air and Water Sealing Components: EPDM and neoprene rubber are used to protect vehicles against external elements in air and water sealing components. These rubber elements, found in doors, windows, and trunks, help keep vehicle interiors dry and clean.
Rubber materials in the automotive sector are indispensable for ensuring durability, safety, and performance. Selecting the appropriate rubber type for each application and adhering to industry standards are critical for the production of reliable and efficient vehicles.