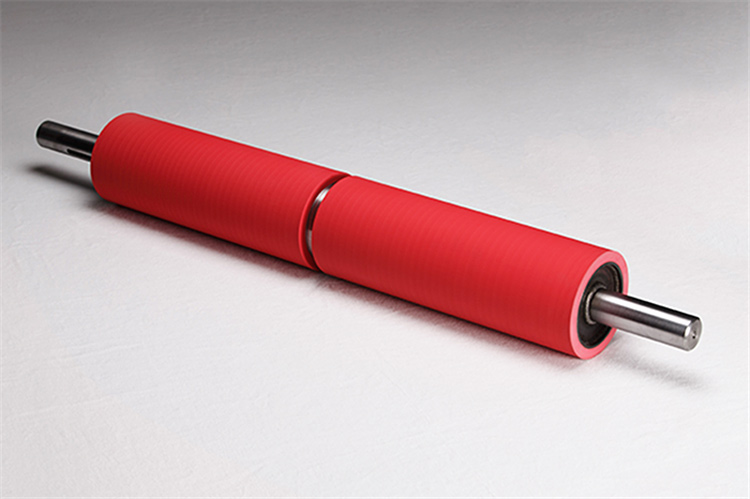
The roller industry is critical for various applications in sectors like printing, textiles, paper, steel, and plastics. Rollers are essential in processes such as compression, surface leveling, coating, and printing. The performance and durability of these processes heavily depend on the reliability of rollers. Rubber materials are widely used in rollers due to their flexibility, chemical resistance, heat resistance, and abrasion resistance. Rubber-coated rollers help protect processed surfaces, enhance print quality, and extend roller lifespan.
Rubber Materials Used in the Roller Industry
Nitrile Rubber (NBR): Nitrile rubber is highly resistant to oils, fuels, and many chemicals, making it ideal for rollers operating in oily environments. NBR-coated rollers are widely used in industries such as textiles, automotive, and printing, where contact with oils is common.
EPDM (Ethylene Propylene Diene Monomer): EPDM rubber offers excellent resistance to ozone, UV rays, water, and certain chemicals. EPDM-coated rollers are frequently used in outdoor environments and water-based chemical applications, such as paper production, textiles, and chemical industries.
Silicone: Silicone is known for its high heat resistance and flexibility. Silicone-coated rollers retain their properties even at elevated temperatures, making them ideal for the plastics and steel industries. Additionally, silicone’s non-stick property prevents materials from adhering to the roller, enhancing process efficiency.
Neoprene (Chloroprene Rubber, CR): Neoprene rubber is resistant to ozone, weathering, and certain chemicals, as well as heat and oil. Neoprene-coated rollers are used in printing and plastic production. Their durability under harsh outdoor conditions makes them suitable for many industrial applications.
Fluoroelastomer (FKM): FKM rubber provides outstanding resistance to high temperatures and chemicals. It is commonly used in rollers for the petrochemical and chemical industries, where it delivers long-lasting performance in high-temperature and acidic/alkaline environments.
Applications of Rubber Materials in the Roller Industry
Printing Rollers: Rubber-coated rollers are used in the printing industry to ensure optimal ink or paint transfer. Silicone and polyurethane-coated rollers provide high-quality printing results by evenly distributing ink and maintaining consistent color transitions.
Textile Rollers: In the textile industry, rollers are used for fabric leveling, compression, and dyeing. EPDM and nitrile rubber-coated rollers are ideal for these processes, as they perform tasks like printing and dyeing without damaging the fabric.
Paper and Packaging Rollers: In the paper industry, rollers are used for flattening and smoothing paper surfaces. Silicone and EPDM-coated rollers provide high durability and surface quality, enabling efficient processing of paper.
Plastic and Steel Industry Rollers: In the plastics and steel industries, rollers are utilized for shaping materials, adjusting thickness, and smoothing surfaces. High-temperature-resistant silicone and polyurethane-coated rollers allow easy processing of plastic and metal.
Chemical Process Rollers: In the chemical industry, rollers must resist aggressive chemicals. Fluoroelastomer (FKM) and neoprene-coated rollers are designed for such environments, ensuring safe and controlled chemical reactions.
Rubber materials are indispensable in the roller industry due to their durability, resistance to harsh conditions, and ability to meet specific application requirements. By selecting the appropriate rubber type, rollers can achieve superior performance, longevity, and reliability across various industrial sectors, ultimately enhancing process efficiency and reducing maintenance costs.