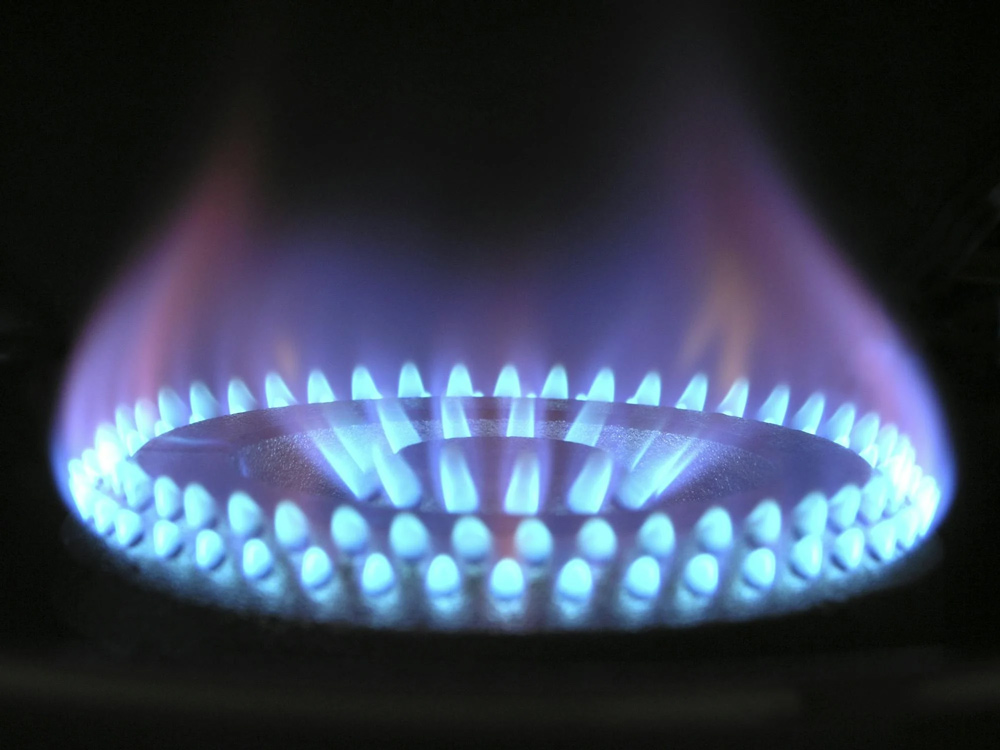
The gas industry requires materials that meet stringent safety requirements and can withstand harsh conditions. In gas transportation, distribution, and storage, rubber materials are essential due to their flexibility, sealing properties, chemical resistance, and ability to operate across a wide temperature range. Rubber materials in the gas sector are governed by standards such as EN549 and EN682, ensuring safety and reliability.
Applications of Rubber Materials in the Gas Industry
Sealing Elements (Gaskets and O-Rings): Sealing is critical for equipment in the gas industry to prevent leaks and ensure safe operation. Rubber materials are widely used for their flexibility in manufacturing sealing components like O-rings, gaskets, and valve seals. These components securely control gas flow and pressure, preventing leaks and ensuring a safe working environment.
Gas Hoses and Pipe Systems: Rubber hoses are ideal for transporting gas due to their durability under high pressure. These hoses, often made from Nitrile Rubber (NBR), are resistant to gas and other chemicals. Their flexibility also allows for easy installation and long-term use.
Sealing Coatings for Gas Storage Tanks: Rubber coatings are applied to the inner and outer surfaces of gas storage tanks to ensure airtight sealing. These coatings prevent gas leakage and enable secure storage within the tanks.
Vibration Dampening Components: Gas facilities often have compressors, pumps, and other equipment that generate vibrations. Rubber materials absorb these vibrations, prolonging equipment lifespan and preventing damage caused by vibration-related stress. Materials such as NBR and EPDM are commonly used for their excellent vibration-dampening properties.
Valve and Regulator Components: Valves and regulators that control gas flow often include rubber sealing elements. These components ensure safe and controlled gas regulation. High-temperature and pressure-resistant materials like FKM (Fluoroelastomer) and HNBR (Hydrogenated Nitrile Rubber) are frequently used in these applications.
Thermal Insulation Materials: Rubber is also used for thermal insulation in the gas industry. Components like gas pipes and tanks are insulated with rubber materials to reduce heat loss and improve energy efficiency. High-temperature-resistant materials such as Silicone Rubber and FKM are suitable for these applications.
Common Types of Rubber Used in the Gas Industry
Nitrile Rubber (NBR): NBR is one of the most commonly used rubber types in the gas industry due to its excellent resistance to gas, oil, and chemicals. It is ideal for high-pressure hoses, gaskets, and O-rings, offering durability and resistance to wear and chemical exposure.
Fluoroelastomer (FKM): FKM is known for its high-temperature resistance and chemical durability. It performs reliably in extreme environments and is often used in valves, regulators, and other components exposed to challenging conditions.
Hydrogenated Nitrile Rubber (HNBR): HNBR offers superior resistance to high temperatures and oxidation compared to standard NBR. It is ideal for applications requiring long-term durability under high pressure and temperature.
Silicone: Silicone rubber is highly resistant to extreme temperatures and retains flexibility even at very low temperatures. It is suitable for high-temperature applications in the gas sector and provides reliable sealing in extreme conditions.
Compliance with Standards in the Gas Industry
Rubber materials used in the gas industry must adhere to strict safety and quality standards to ensure reliable performance. Standards such as EN549 and EN682 evaluate the compatibility, durability, and safety of rubber materials in gas-related applications, guaranteeing their suitability for critical environments.
Conclusion
Rubber materials play an indispensable role in the gas industry by providing reliable sealing, durability, and flexibility. Their ability to withstand extreme conditions and meet safety standards makes them essential in gas transportation, distribution, and storage. Choosing the right type of rubber material ensures efficient, safe, and long-lasting performance in this demanding sector.